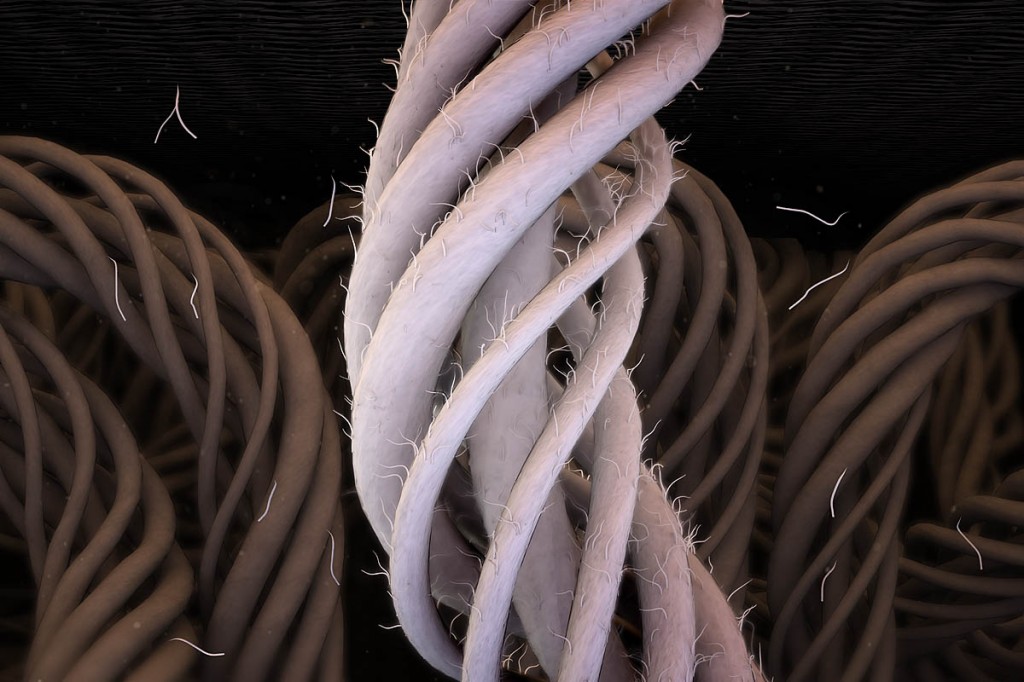
Polartec's Lightweight Power Air significantly reduces the microfibres released into the environment
For the conscious adventurers among us, our appreciation of the outdoors is being muddied with our concern over the frequent news of our impact on it. And none more so at the moment than the clothes we wear. The energy and water consumption that goes into producing and using one garment of outdoors wear has a huge effect on the very nature we’re trying to enjoy.
Sponsored feature
It’s a theme that’s influencing new sustainable design goals for many outdoor brands. The use of recycled materials in our fabrics, a focus on repairing rather than replacing, and developing durable fabrics with long lifespans are all top of the agenda. Manufacturers, like Polartec, for example, have already recycled over a billion plastic bottles into fleece material.
Clothing and shoe production stands for 8 per cent of the world’s greenhouse gas emissions – that’s more than all air and water transport combined. The textile industry is also responsible for 20 per cent of all water pollution globally. And in particular, the relative new issue of microplastics and microfibres is hitting headlines daily.
Microfibres are the tiny fibres which are easily shed from fabrics during normal day to day wear, or, in particular, when we wash them. Natural fibres like wool and cotton will biodegrade in the environment, but polyester and other synthetic fabrics are basically plastic – which won’t. The problem is microfibres are so small they can literally get everywhere. In particular through our sewage systems, filtering systems and out in the oceans – where they’re consumed by plankton and travel up the food chain at an alarming rate. Although the science is still too new on how this affects our health as humans when we eat fish, we do know that microplastic can fill a fish’s stomach, get stuck there and eventually kill the fish. So much so that in 2018 microbeads were banned from health products.
But polyester has its place in the outdoor industry. It is incredibly durable, so any product made from it lasts a long time; it also has great weatherproofing properties and, made the right way, it can be produced from recycled plastics and become fully recyclable itself.
That’s where companies like American material manufacturers, Polartec, are coming to the fore. You may not have heard of Polartec, or you may ask for it by name whenever you buy any outdoor wear from Rab, Arc’teryx, Mammut, Patagonia or Norrona for example. That’s because they don’t sell direct to the consumer, they produce fabrics and materials which are bought by premium outdoor clothing designers. In the same way that brands choose to use GORE-TEX or Nikwax Hydrophobic Down within their clothing ranges.
In 2018, Polartec launched Power Air. An ingenious insulation material that works a little like bubble wrap! After recognising that any exposed fibres are susceptible to shedding, it looked to designing a fabric which encapsulates lofted microfibres actually inside the knitting process.
This manufacturing design results in Power Air shedding five times fewer microfibres than other premium midlayer fabrics. It also works to trap air and generate heat, making it incredibly warm yet breathable. The goal for outdoor enthusiasts who don’t want to have to remove layer upon layer the harder they work.
Power Air is the culmination of a multi-year development consisting of thousands of work hours and dozens of iterations and is the latest product of Polartec Eco-engineering. Eco-engineering is the process by which Polartec deploys recycled inputs, advanced production techniques, highly efficient logistics, and rigorous testing and certifications to create an unrivalled innovation pipeline devoted to producing sustainable fabrics with elite performance characteristics.
Polartec’s CEO, Steve Layton, said: “By using the efficiency of encapsulated air to shelter lofted fibres, Polartec Power Air will drastically improve how fabrics perform over their lifetime with respect to versatility, comfort, and sustainability. We’re only beginning to realise the potential for this new type of fabric construction.”
Mike Rose, their VP of Product Development added: “Polartec has never shied away from solving tough, intractable problems. Power Air has the potential to be our most significant development since pioneering the process to knit fabrics made of post-consumer plastic bottles.”
And now this year they’re launching a lighter weight version. Lightweight Power Air adds to Polartec’s environmental credentials because it’s also fully recyclable and made from 73 per cent post-consumer plastic waste. This means the raw material never has to be waste again; and Polartec is helping to reduce the waste we do have.
The first product to the market comes from Swedish outdoor sportswear company, Houdini. Its Mono Air Houdi is a light and airy yet wonderfully warm insulation jacket that you can wear all year around. The low-friction surface makes it perfect to layer under your shell jacket in the winter. And the breathable fabric provides the perfect temperature on its own during a chilly summer evening. The fit of the jacket is based on the Iconic Houdini Power Houdi (which features Polartec’s original Power Air), with a slim fit style, a snug high collar hood and extended sleeves with thumb loops.
Houdini said: “The Houdini Mono Air Houdi and Power Air fabric platform from Polartec opens the door to the next generation of sustainable fleece garments. The project is part of Houdini’s quest to become a regenerative force for good in the outdoor industry steered by the vision of doing good, playing hard, having fun and pushing boundaries.”
More details can be found on the Polartec website.